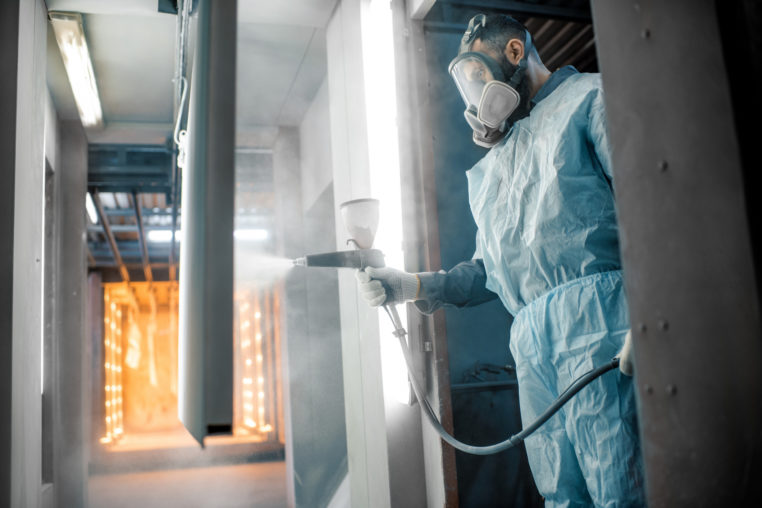
What Is a Finish?
Nearly every product that undergoes a manufacturing process has a finishing process that’s designed to improve its appearance, durability, or other factors. A finish may also be applied to antique or deteriorated products in order to salvage or repair them.
Learn more about finishes and how they make every product look better and last longer.
Industrial Finishing
Surface finishing is used in a broad range of industrial processes, such as automotive, marine, aerospace, military, recreational vehicles, household appliances, and more, as the last stage of the production process.
The primary purposes of finishing are to provide a protective coating for tarnish resistance, corrosion resistance, chemical resistance, wear resistance, and hardness, and to make the final product more aesthetically appealing by removing surface flaws or irregularities. Finishing may also be used to make a product more flexible or to give it a colored or high-gloss appearance, such as with automotive components.
High-quality finishes are particularly important with outdoor products, such as vehicles, lawn furniture, and outdoor home accents, since they experience a lot of inclement weather conditions and ultraviolet radiation from the sun that can degrade the surface over time. Cars, trucks, boats, recreational vehicles, lawnmowers, and motorcycles are particularly susceptible to rust from moisture and to scratches and dings from road debris, so having a surface finish helps to protect against these unsightly problems.
Finishes for Aesthetics
Though the protective properties are the most important aspects of a finish, many finishing techniques offer an additional aesthetic appeal. Finishes can be smooth, textured, matte, metallic, wrinkled, glossy, high-gloss, and even pearlescent, as well as coming in virtually every color of the rainbow. Some finishes even have ombre effects or other color effects to enhance the look.
Regardless of the look of the finish, adding a finish with decorative effects doesn’t diminish the protective qualities of the finish itself.
Types of Finishes
Though there are many types of finishes on the market, the most common finishing types used in manufacturing today are liquid paint, powder coating, and electrocoating.
Liquid Paint
Liquid paint is commonly used in industrial processes and can be applied to many different surfaces. In manufacturing environments, liquid paint is usually applied with a robotic system.
With liquid paint, the paint color is suspended in a liquid binder made of solvents, pigment, and several curing agents. Using a pressurized canister, the paint is sprayed onto different parts in an even coating. Low heat or air allow the liquid binder to evaporate, leaving only the paint behind.
Unfortunately, liquid painting has some significant disadvantages, such as dripping, cracking, peeling, and toxic fumes, regardless of how diligently the paint is applied.
Powder Coating
Powder coating is a type of dry finishing process that was only introduced in the 1960s, but it’s become incredibly popular in the industrial finishing market. Powder coating can be used on a wide array of products for a durable, high-quality finish that’s both decorative and protective.
Powder coatings are based on a polymer resin system combined with curatives, leveling agents, pigments, flow modifiers, and other additives. These ingredients are mixed, cooled, and ground into a uniform powder to be applied to a surface with a process called electrostatic spray deposition.
This process begins with using a spray gun that applies an electrostatic charge to the powder particles, which become attracted to the grounded metal product to be finished. After application, the product enters a curing oven where the coating chemically reacts to produce long molecular chains and high cross-link density that’s resistant to breakdown. Powder coating can also be applied to non-metallic surfaces with different techniques.
The main advantage of powder coating is the high-quality, consistent finish that completely saturates the rough or uneven surfaces of machinery or household items. Its finish is more durable than other methods, and it’s resistant to ultraviolet light, chemicals, moisture, impact, and extreme weather conditions, making it ideal for products that will experience inclement weather or that are subject to a high risk of chipping, abrasion, scratching, corrosion, fading, or other types of wear.
Another advantage of powder coating is that it comes in virtually limitless colors and finish types, so it’s even more versatile than liquid paint. Because of this, powder coating is popular in the automotive industry.
Powder coating is also simple to use, cost effective in the manufacturing process, and environmentally friendly, since little product is wasted during the process. Because it’s a dry product, excess powder can be collected and reused easily.
Electrocoating
Electrocoating is similar to powder coating in that it uses electrically charged particles to create a bond on a conductive product. During the electrocoat process, paint is applied to a product at a certain thickness, which is regulated by the voltage applied. The application is self-limiting and slows as the product is electrically insulated, so there’s little waste.
During the electrocoat process, the products are cleaned and pretreated for application, then dipped into a paint bath with a direct current applied between the products and a counter electrode. The paint becomes attracted to the electric field and is deposited on the product, which is then removed, rinsed, and baked to cure.
Though electrocoating provides total coverage in a cost-effective and environmentally friendly manner, the ultra-thin layer of deposited paint is not nearly as durable as other finishing techniques. It’s also not ultraviolet-resistant, so it’s not suitable for outdoor products and may require an additional topcoat, which increases the cost and time involved in production.
Visit AR Powder Coating
There you have the basics of industrial finishing and the types of finishing available. Though different coatings are used for different industrial processes, powder coating is growing in popularilty for its cost-effectiveness, efficiency, and environmental safety, especially in large-scale manufacturing. Powder coating has proven time and time again to outlast other coating types in industrial finishing applications.
At AR Powder Coating, we understand the value and versatility of powder coating in industrial finishing. We offer both batch and conveyor production coatings to handle any size manufacturing job, along with unlimited color options with a durable, corrosion-resistant finish. Contact us today to learn more about our industrial powder coating and get your estimate!