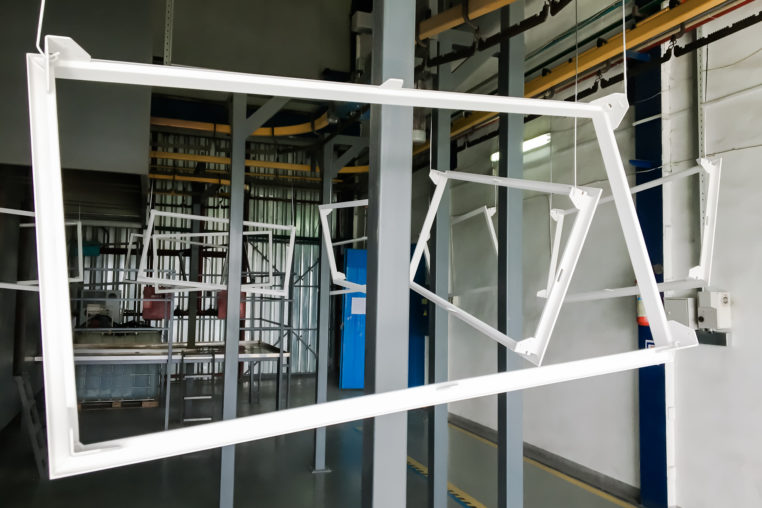
What is Outgassing in Powder Coating?
In this post, we’ll break down the causes of outgassing and pinholes while powder coating, and go over some of the ways that AR Powder Coating combats this phenomenon.
What Is Outgassing in Powder Coating?
Outgassing is a defect that can occur in powder coating. It can be explained by one or possibly several different problems with powder coating the project at hand. When objects are heated prior to powder coating, superficial and internal contaminants can rise to the surface of the material, then burst through the powder coat. These bursts are called “pinholes.”
Pinholes create both a cosmetic defect and an opportunity for damage to the project as pinholes allow water to seep in through the powder coat, which allows rust or other corrosion to occur to the base metal of the object.
What are Pinholes?
Pinholes are exactly what they sound like: tiny holes in the surface of powder-coated material, about the size of the head of a pin. They are a common outgassing problem in powder coating, because they not only mar the surface and make the powder coat quite unattractive, but they can let moisture and other corrosive materials in through the powder coat.
What Causes Pinholes?
Pinholes are caused by any number of problems in the powder coating process. The most common are:
Surface Contamination
We make a big deal out of cleaning and prepping our projects here at AR Powder Coating, and the number one reason is to avoid pinholes and bubbles. Pinholes are often caused by surface contamination: which is what happens when you don’t clean your project thoroughly before powder coating. Oil, grease, and other forms of contamination left on the surface turn into gas under high heat and have nowhere to go when they are trapped by the powder coat, so they simply burst through, creating pinholes.
Thickness of Coating
Coatings should be applied in thin layers; when you apply a thick coat, even if the project warrants one, gasses can be given off during the curing process and make their way to the coating’s surface. It’s essential to have a working knowledge of the materials used in powder coating so that you can make necessary adjustments to ensure the coating thickness doesn’t contribute to pinhole problems.
Castings
Cast metal is a commonly-used base for powder coating projects. The problem with cast metal is that it can give off a lot of gasses during the powder coating process. This is because oftentimes, the casting process itself traps gasses in the metal.
Galvanization
Galvanization happens when highly-corrodible steel is coated with a layer of zinc in its manufacturing process to combat corrosion. That layer of zinc often traps gasses between the zinc and the steel. Plating steel with zinc is great for combating corrosion, but not so great for powder coating.
How to Fix Existing Pinholes?
Once pinholes happen, they are tough to fix, but here are a couple different things you can try:
Re-Coat the Part
You can try reheating and recoating the part to see if another layer of powder coat resolves the pinholes.
Strip It Completely (Or Re-Blast It)
Go back to the very beginning of the project by stripping off all of the layers of powder coating and try again. Make sure you prep slowly and carefully. By doing so, you may be able to achieve a perfect powder coat the 2nd time around.
How is Outgassing Prevented?
Outgassing can be prevented by properly prepping your materials, knowing the right substrates to use for the powder coating process, and handling your materials properly. These are the steps:
Clean all Contamination
Clean and degrease the object you’re powder-coating thoroughly and carefully. Make sure to wear gloves so that your hands don’t leave oils on the surface of the project’s base.
Control the Thickness of the Powder Coat
Some jobs require a heavier coat than others, but it doesn’t have to be applied in one coat. By understanding the materials used in the coating and using multiple coats if necessary, outgassing caused by applying too thick a powder coat to your project can be avoided.
Use a Primer
Applying a sealant as a primer coat before powder coating helps to ensure that any gasses released during the heating process are contained by the primer. They will be unable to bubble up into the powder coating itself. This is not considered a replacement for thorough cleaning and decontamination.
Incorporate Additives
The gasses escape through the coating as the coating itself is hardening, which causes the pinholes. Certain additives may be employed that cause powder to remain in liquid form for longer. This will give the gasses more time to escape before the powder hardens.
Preheat the Part
Since outgassing is caused by gasses being released when the object is heated, it can be avoided by heating the object before the coating process begins. All of the gas bubbles can then expel themselves from the material before the powder coating phase begins.
Get the Job Done Right The First Time With AR Powder Coating
Knowing all of the ways that problems like outgassing can pop up is key to a successful powder coat. At AR Powder Coating, our decades of experience enables us to foresee problems not only with outgassing, but the various other issues that can crop up.
If you are looking to have a powder coating job completed, please feel free to contact us today with any questions you have. We look forward to doing business with you.