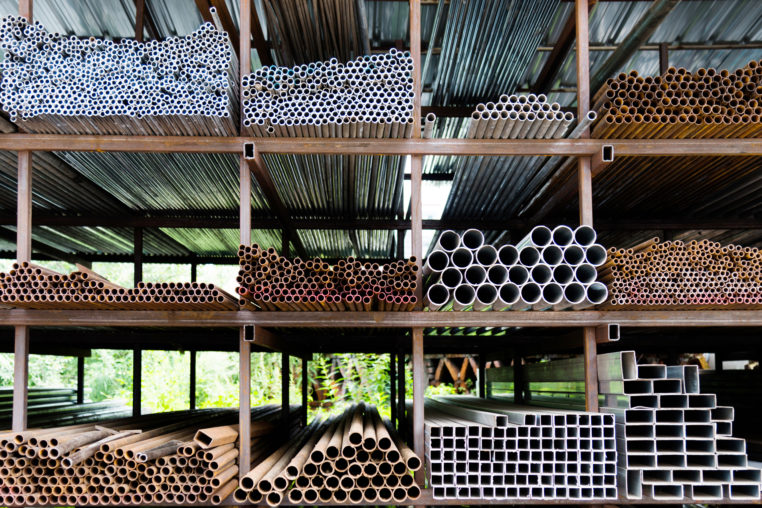
The Applications and Benefits of Powder Coating for Industrial Steel Fabrication
Powder coating is among the easiest ways of protecting different equipment and objects. More manufacturers are adopting this technology due to its numerous benefits. It does not have any solvents in the contents since it does not require a binder to remain in a liquid state. Most of the time, it would make more sense than coating with the aid of liquid paint.
This exhaustive piece covers the industry applications and benefits of powder coatings.
What is powder coating?
This advanced technology is used for applying a protective and decorative finish to virtually any metal variety used by both consumers and industries. The powder used comprises a finely-ground mixture of resin and pigment. It is usually sprayed electrostatically onto any surfaces meant for coating.
The process releases charged particles that stick on electrically grounded surfaces via adhesion. The painted surface is then taken to the curing oven, where it stays until the powder heats and fuses into a smooth coating. The end result comprises of high quality, durable, uniform, and attractive finish. Due to its efficiency, it has grown to be among the finishing technologies with the fastest-growing popularity.
Notably, this technology represents over 15 percent of the entire industrial finishing sector. It is used for decorative and functional (protective) finishes. Furthermore, you can choose from a nearly limitless range of textures and colors, and technological advancements have ensured excellent performance properties.
That explains why the technique is used in different industries for a range of products.
Industry application of powder coating
Here are some of the key industries that use the innovative finishing process:
Appliances
This industry is one of the key beneficiaries of powder coating. It is used on the side and front panels of a variety of refrigerators, washer lids and tops, air conditioner cabinets, dryer drums, dishwasher racks, microwave oven cavities, and water heaters. Furthermore, powder coating has grown to be an effective and popular replacement for porcelain enamel on a range of dryer and washer parts.
Construction/architecture
In the building and architectural sector, the process is used to coat aluminum extrusions for frames of doors and windows, as well as on modular furniture. Currently, most buildings and highway construction projects rely on powder coats. It is used on guardrails, light poles, posts, signs, and fencing.
Automotive
The automotive sectors use powder coatings on door handles, bumpers, wheels, hubcaps, truck beds, filters, radiators, different parts of the engine, and sections with decorative trim and accent. Also, a clear powder topcoat is always applied for the protection of auto bodies. For instance, Volvo and BMW have adopted the technique and are currently using it on their latest model cars.
Ford, Chrysler, and GM have established a consortium aimed at testing the technology on their respective production lines.
Day to day products
Powder-coated products have enumerable day to day uses. These include antennas, lighting fixtures, and a range of electrical components. Fitness buffs utilize golf carts and golf clubs, snowmobiles, ski poles and bindings, bicycles, and training equipment. All these are powder coated. Farmers also benefit through the use of powder-coated farm equipment and tractors.
Shop owners are not left behind with their powder-coated shelves, vending machines, store fixtures, and display racks. You will also come across office workers using computer cabinets, metal furniture, thumbtacks, mechanical pens and pencils, and numerous desk accessories coated with powder. Parents use cribs, baby strollers, wagons, and baby toys that have been passed through the same technique.
Homeowners, also, have snowblowers, lawnmowers, barbecue grills, garden tools, bathroom scales, electrical components, fire extinguishers, and toolboxes. All these items benefit a great deal from their powder coating finishes.
Top benefits of powder coatings
Among the available methods of painting equipment and parts, powder coating stands as the most popular. Here are some of the key benefits that make it stand out over any traditional painting method:
- Durable – When it comes to the finish, this stands out as the most durable protection. When curing, the powder melts then gels together while forming long chemical chains. Consequently, the finish ends up more flexible, allowing for a small amount of flexing and bending as parts move and vibrate. Furthermore, it is resistant to corrosion, flaking, and scratching.
- Efficient – The powder is held to the part using electrostatic charges, and the process creates minimal waste. Also, your specialist may use as little or as much powder as necessary for a single application. Instead of waiting for every coat to dry before you apply the next, everything is completed once, and curing takes place evenly.
- Cost-efficient – The process eliminates additional steps and drying time, and any material used is acquired as per the size specifications. Also, the powder is cheaper than wet paint and requires less storage space. In the end, powder coating stands out as the most cost-efficient.
- Variety – You can choose any of the common finishes and colors for your item. Even better, it allows for their complete customization. Manufacturers come up with special powder blends to match any color as well as texture options like adding glitter, or wrinkles. Very few options could beat this versatility and range.
- An environmentally friendly option – The powder used in this process is free from harmful solvents or volatile organic compounds. Hence, it is recognized as safe to use and dispose of. This process also produces fewer wastes with no harmful chemicals released into the atmosphere. However, painters are advised to avoid inhaling the powder and have protective gear on to avoid skin contact.
- Overall quality – From application to curing, the process leads to an unmatched quality finish. The powder usually melts and flows together across the entire unit, creating an even surface. This end product is not subject to dripping, running, or unevenness that characterizes wet paints. So sanding or refinishing is not necessary whenever a mistake has been made.
- Maintenance – The final benefit of powder coating is its extremely easy maintenance in the long run. No solvents or special cleaners are required to keep it clean as you can use regular soapy water. Also, rust should not worry you since the coating can resist scratching or corrosion.
From all these applications and benefits, you can see the many ways in which power coating beats traditional options. With the proper equipment, the process minimizes finishing time, creates better quality finishes, and offers a wide range of color or texture choices. The option is also eco-friendly and more cost-effective.
If you need quality and sufficient industrial power coating services, then AR Powder Coating has everything you need. Contact us today for a wonderful experience and satisfaction.