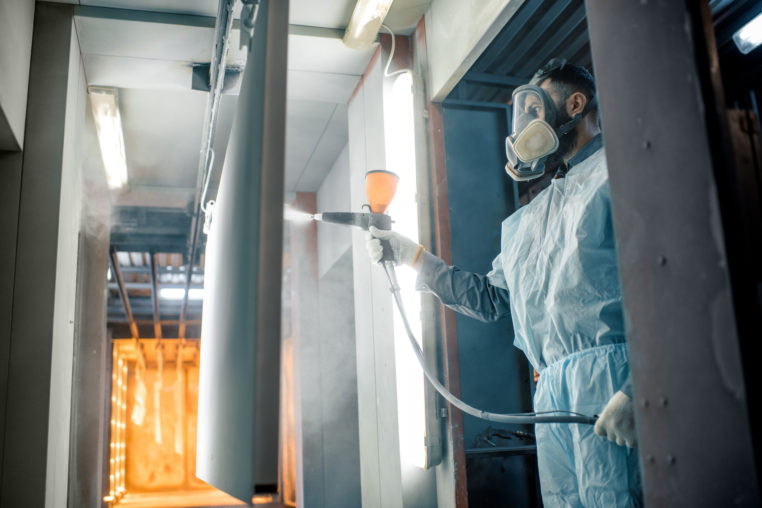
Powder Coating vs. Zinc Plating: Which Is Better?
When it comes to powder coating and zinc plating for metal finishing, both methods offer distinct advantages in protecting and enhancing metal surfaces, but a deeper dive reveals significant differences. Powder coating, known for its robust protection and vast color options, offers enhanced durability and an eco-friendlier approach. This article delves into the nuances of each method, providing insights that point toward powder coating as the superior choice for a variety of applications.
Key Takeaways
|
Understanding Powder Coating
Powder coating is a highly effective and popular method for applying a protective and decorative finish to various metal surfaces. Unlike traditional liquid paint, powder coating involves the use of a fine, dry powder made up of finely ground particles of pigment and resin. This powder is electrostatically charged and then sprayed onto the metal surface, creating a uniform and adherent coating.
How the Process Works
The powder coating process consists of several key steps:
- Surface Preparation: Before the powder coating can be applied, the metal surface must be thoroughly cleaned and prepared. This involves removing any contaminants, such as oils, rust, or old paint, to ensure proper adhesion.
- Application: Once the surface is prepared, the dry powder is electrostatically charged. The positively charged powder particles are attracted to the negatively charged metal surface, ensuring an even and uniform coating.
- Curing: After the powder is applied, the coated metal is placed in an oven, where it undergoes a curing process. During curing, the powder particles melt and fuse together, forming a continuous, durable, and smooth finish.
Benefits of Powder Coating
Powder coating offers a multitude of advantages that make it a preferred choice for finishing metal surfaces:
- Durability and Resistance to Corrosion: Powder-coated surfaces are exceptionally durable and resistant to various forms of damage. They can withstand exposure to harsh environmental conditions, including moisture, UV rays, and chemicals, without deteriorating or corroding. This durability ensures that the coated metal maintains its integrity and appearance over an extended period.
- Wide Range of Color Options: Powder coating provides an extensive palette of colors and finishes to choose from. Whether you desire a vibrant, glossy finish or a subdued, matte appearance, powder coating can accommodate your aesthetic preferences. This versatility allows for creativity in design and the ability to tailor the finish to your specific requirements.
- Eco-Friendliness: Powder coating is recognized for its environmental benefits. Unlike traditional liquid coatings that often contain volatile organic compounds (VOCs), powder coating is solvent-free and emits minimal pollutants. The overspray from the powder application can also be collected and reused, reducing waste and conserving resources. Additionally, the absence of harmful chemicals makes it a safer option for both the environment and those involved in the application process.
Examples of Suitable Applications for Powder Coating
Powder coating is a versatile finishing method suitable for a wide range of applications across various industries. Some common examples include:
- Automotive Parts: Many automotive components, including wheels, frames, and engine parts, benefit from the durability and corrosion resistance of powder coating.
- Architectural Structures: Powder coating is commonly used to finish architectural elements such as railings, gates, fences, and outdoor fixtures. Its resistance to weathering ensures that these structures remain attractive and intact over time.
- Appliances: Household appliances, such as refrigerators, ovens, and washing machines, often feature powder-coated finishes that enhance their appearance and protect them from wear and tear.
- Furniture: Powder coating provides both aesthetics and durability to metal furniture, making it suitable for indoor and outdoor use.
- Industrial Equipment: Machinery and equipment in industrial settings benefit from powder coating’s protective properties, ensuring longevity and efficient operation.
- Sports and Recreational Equipment: Items like bicycles, playground equipment, and gym machines are frequently powder-coated for their resistance to rust and visual appeal.
Understanding Zinc Plating
Zinc plating, also known as galvanization or zinc electroplating, is a widely used surface finishing process that involves the application of a layer of zinc onto the surface of a metal substrate. This process is aimed at providing a protective and corrosion-resistant coating to the base metal, primarily iron or steel, to enhance its longevity and prevent corrosion.
How the Process Works
The zinc plating process consists of the following essential steps:
- Surface Preparation: As with any surface finishing process, the initial step involves thorough surface preparation. The metal substrate is cleaned meticulously to remove dirt, grease, rust, and any other contaminants that may hinder the plating process.
- Electrocleaning: Following the initial cleaning, the metal substrate undergoes an electrocleaning process. This step ensures that the surface is free from any remaining impurities and is electrically conductive.
- Acid Pickling: In this step, the metal is immersed in an acid solution to further remove oxides and scale, allowing for better adhesion of the zinc coating.
- Zinc Plating Bath: The cleaned and prepared metal is immersed in a specialized bath containing a zinc salt solution. An electric current is applied, causing the zinc ions to migrate to the metal’s surface and form a layer of zinc on the substrate through an electrochemical process. The thickness of the zinc layer can be controlled by adjusting the duration of plating.
- Rinsing and Drying: After plating, the metal is thoroughly rinsed to remove excess plating solution. It is then dried to prevent water spots and ensure a uniform appearance.
- Passivation: Optional passivation is performed to further enhance the corrosion resistance of the zinc coating. Passivation involves applying a protective layer, often a chromate or other chemical compound, over the zinc layer.
Advantages of Zinc Plating
Zinc plating offers several advantages, making it a popular choice for protecting metal surfaces:
- Corrosion Protection: Zinc plating provides excellent corrosion protection to the underlying metal substrate. It acts as a sacrificial anode, meaning that the zinc coating corrodes in preference to the base metal, thus preventing rust and corrosion from affecting the substrate.
- Cost-Effectiveness: Zinc plating is a cost-effective method for protecting metal surfaces, making it an attractive choice for industries where cost considerations are paramount. The process is relatively straightforward and can be applied to a wide range of metal parts and components.
- Electrical Conductivity: Zinc-plated surfaces retain good electrical conductivity, making it suitable for electrical and electronic applications where electrical contact is essential.
Suitable Applications for Zinc Plating
Zinc plating finds numerous applications across various industries due to its protective and cost-effective properties. Some common applications include:
- Fasteners: Bolts, screws, and nuts are often zinc-plated to protect them from corrosion and improve their lifespan.
- Automotive Components: Many automotive parts, such as brake calipers, brackets, and exhaust components, are zinc-plated for corrosion resistance.
- Hardware: Various hardware items, including hinges, handles, and brackets, benefit from zinc plating to ensure durability and prevent rust.
- Electrical and Electronic Components: Zinc plating is used in electrical connectors and components to provide corrosion protection while maintaining electrical conductivity.
- Construction Materials: Steel beams, brackets, and other construction materials are often zinc-plated to withstand exposure to the elements.
Comparing Powder Coating and Zinc Plating
When it comes to surface finishing for metal products, the choice between powder coating and zinc plating can greatly impact the durability, aesthetics, environmental impact, cost, and overall customer satisfaction. Let’s delve into a detailed comparison of these two methods across various aspects:
1. Durability and Corrosion Resistance:
Powder CoatingPowder coating excels in providing exceptional durability and corrosion resistance to the underlying substrate. The cured powder forms a tough, protective barrier that shields the metal from environmental elements, such as moisture, chemicals, and UV radiation. |
Zinc PlatingZinc plating is also known for its corrosion resistance. However, it operates as a sacrificial anode, meaning that the zinc layer corrodes in place of the base metal. This method effectively protects the substrate from rust and corrosion. |
Winner: Both methods offer strong protection against corrosion, but powder coating may have a slight edge in terms of its resistance to a wider range of environmental factors.
2. Aesthetics and Customization:
Powder CoatingPowder coating provides a wide spectrum of color options and finishes, allowing for extensive customization. Glossy, matte, textured, or metallic finishes are readily achievable, making it a preferred choice for enhancing the visual appeal of products. |
Zinc PlatingZinc plating primarily provides a silver or gray metallic appearance, which may not offer the same level of aesthetic customization as powder coating. |
Winner: Powder coating clearly wins in terms of aesthetics and customization options, allowing for a broader range of visual styles.
3. Environmental Considerations:
Powder CoatingPowder coating is considered an eco-friendly finishing method. It generates minimal waste as excess powder can be collected and reused. Additionally, it produces no harmful volatile organic compounds (VOCs) or toxic fumes during curing, making it environmentally responsible. |
Zinc PlatingZinc plating involves the use of chemicals, including acid pickling and plating solutions, which can raise environmental concerns. Proper disposal and treatment of these chemicals are essential to mitigate environmental impact. |
Winner: Powder coating is the more environmentally friendly choice, with a smaller ecological footprint.
4. Cost-Effectiveness:
Powder CoatingWhile powder coating offers excellent protection and customization, it may have a slightly higher initial cost due to equipment and material expenses. However, its long-term durability can lead to cost savings by reducing maintenance and replacement needs. |
Zinc PlatingZinc plating is known for its cost-effectiveness. The process is relatively straightforward and requires less equipment, which can translate into lower upfront costs. |
Winner: Zinc plating tends to be more cost-effective initially, but long-term cost considerations may vary depending on the application.
Choosing AR Powder Coating: The Superior Surface Finishing Solution
When it comes to surface finishing for metal products, powder coating emerges as the ultimate choice. It offers exceptional durability, corrosion resistance, and a wide range of customizable colors and finishes. Powder coating’s eco-friendly attributes and long-term cost-effectiveness set it apart as the superior option.
Ready to enhance your metal products with the excellence of powder coating? Contact AR Powder Coating today for top-quality finishing that combines aesthetics, durability, and sustainability.