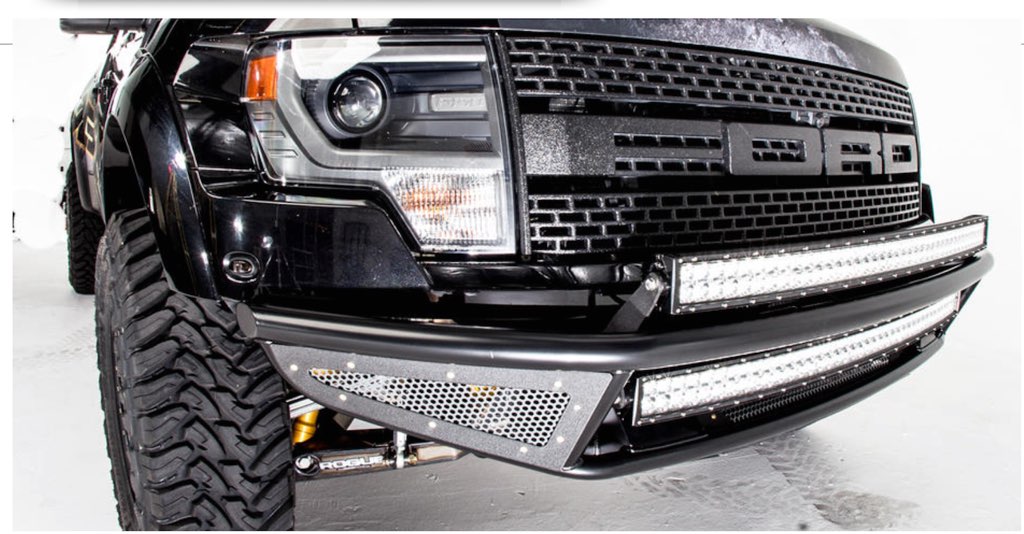
How Powder Coating Transformed the Automotive Industry
For many years, conventional liquid coatings were the industry standard for automobiles. These coatings can emit volatile organic compounds during application that have serious consequences for both the environment and human health.
Unlike conventional liquid coatings, powder coating doesn’t use solvents, so there are no harmful emissions released into the atmosphere. Powder coating also protects against overspray, allowing powder to be collected and reused for more cost effectiveness. Finally, because powder doesn’t run or drip like liquid, it provides a uniform, high-quality finish that other coatings just can’t match.
Discover the many ways powder coating transformed the automotive industry and how it’s become the industry standard for a variety of applications.
A Brief History of Powder Coating in the Automotive Industry
The underhood segment of the automotive industry was the first to apply powder coatings and release the benefits of this technology.
Beginning in the early 1970s, thin-film epoxy powders were used for corrosion resistance on coil springs. The challenge was finding a coating that allowed coil springs the optimal flexibility, while also providing protection for the extreme environment within a vehicle’s mechanical components. Once implemented, this early form of powder coating provided components with excellent field durability without compromising their performance. Soon, everything from stamped steel brackets to tubing received powder coating to benefit from the corrosive- and chemical resistance of this protective finish.
Powder coating evolved to engine blocks and cylinder heads as well. The previous process of painting an engine used to involve sending an assembled engine through a liquid paint booth, with careful masking to avoid over-sprayed paint from finding its way into the intake manifold and flywheel. Pretreatment and cleaning was difficult at best, and finished part performance left a lot to be desired.
Powder coating offered many advantages over this old painting process. The blocks and heads were painted immediately after the casting process, which avoided the cleaning step. Raw castings naturally have a lot of texture as well, so the powder adheres to the block without the need for pretreatment. The resins used in powder coating have a higher molecular weight, providing a higher-quality finish for treated parts.
With the engine’s weight, however, specialized coating lines had to be developed to handle the weight of the engine and the curing ovens used to crosslink the powder. Despite these challenges, powder coating proved to be a beneficial and economical solution for manufacturers, providing outstanding finished part durability and the ability to recover overspray to limit waste. Powder coating took place as the castings move from the foundry to the assembly plant as well, which reduced transportation costs, and the coating showed the necessary integrity to withstand the machining process.
Powder coating also revolutionized the wheel market. Cast aluminum wheels were the industry standard in the 1980s, marketed almost exclusively in the aftermarket to customers who took incredible care of their vehicles. Because they weren’t experiencing an extreme environment, many of these wheels left the line with no protective clear coat at all. It wasn’t until they were distributed all over the nation that a protective clear coat would be used, which was solvent-based and presented a hazard to the environment. Because of this, the production of wheels was restricted according to air quality permits.
In an effort to comply with air quality regulations, the automotive industry searched for an alternative to these VOC coatings. Clear powder coats were the answer to meet demands, but manufacturers quickly discovered other advantages. Because powders could provide a smooth finish on the most complex wheel shapes, fewer wheels were rejected. Powder also goes on thicker than liquids, providing additional edge coverage and better overall corrosion protection.
It wouldn’t be long before metallic powders and other decorative powder effects began dominating the market. Unlike with their previous options, those looking to enhance their vehicle’s appearance could benefit from flashy finishes without compromising the corrosion resistance and durability they needed.
Today, a powder basecoat with a powder clearcoat is still the most durable and attractive paint finish for aluminum wheels.
Powder Coating in Modern Vehicles
The early powder coating process hasn’t changed much, but the technology and applications have. In modern vehicle design, the engine compartment can be a decorative element of a vehicle. Cast-aluminum intake manifolds and fuel injection systems have a tidier appearance and dominate much of the engine compartment, leading to powder coating becoming a dual-purpose coating for aesthetic appeal and protective qualities. Highlighting casting with powder coat gives it a uniform appearance and the durability to keep the manifold looking new throughout many miles, as well as hiding any imperfections in the casting.
It wasn’t long before the attractive appearance of powder coating was applied to the interior and exterior trim parts. A single coat of powder is usually applied to the interior structural elements to provide corrosion resistance, but the more exciting finishes are reserved for interior accents. Trim pieces, speaker grilles and other elements found at or above the beltline, where they’re most likely to receive UV exposure, are treated with a low- or high-gloss coating to give them an attractive finish and help them resist fading and discoloration.
Exteriors showcase some of the best powder coating applications in the industry. The ultra-popular “blackout” look is a result of powder coating, which puts matte or gloss black powder onto grilles, emblems, window trims and other accents to give the vehicle a sharp, streamlined appearance. These parts are typically “add-on” parts as well, so they benefit from having a finish that’s as durable as the body coating materials and offers a seamless blend once fitted to the vehicle.
Some door handles are made from zinc die-castings, which required a different kind of powder coat and would be the beginning of commercialized powder coating for vehicles. The first specification for this process, pioneered by GM, outlined a specific process for cleaning, priming and top coating zinc castings with polyester-urethane powders. These powders were then used for steel and aluminum moldings, often without the need for priming, and are still the most widespread today and represent the best combination of durability, appearance and cost effectiveness.
Powder coatings came out of the gate offering more than their liquid coating counterparts could compete with, but they still evolved to become more durable and longer-lasting. Polyester-urethane coatings have excellent performance, but an enduring problem was the loss of the high-gloss finish after prolonged sun exposure. Acrylic powders, which have better weathering characteristics, were a logical progression, and combined with the existing acrylic chemistries of body basecoat and clearcoat systems.
Looking to the Future
Despite the considerable benefits that powder coating has already brought to the automotive industry, we’ve barely scratched the surface of the possibilities.
The extent of powder coating for vehicle bodies has been its use as a primer-surfacer, which is part of the production in several automotive assembly plants. Countless others use powder coats as a resistant coating for the leading edge of sheet metal and rocker panels, both of which are prone to chipping and cracking. Still, the full-body application of powder coating remains limited, though it’s growing in importance. As a primer-surfacer, powder coating protects the underlying electrocoat primer from UV degradation and provides superior chip resistance for the paint system, as well as being an economical and environmentally friendly alternative to liquid coatings.
As the technology grows, powder coating can prove to be a high-quality protective and decorative clearcoat for the body, substituting the conventional liquid clearcoats. By protecting the finish from rain deposits, UV exposure, road debris and weather damage, powder coating has the potential to keep vehicles looking “showroom quality” for much longer.
There’s also market potential for high-heat-resistant powder coating for aftermarket exhaust systems. This is already in production for some aftermarket parts, but the corrosion resistance, chip resistance and ability to prolong the life of the system has incredible potential for the whole of the new-car market.
The most promising growth potential for powder coating in the automotive industry comes from plastic surfaces, however. Plastic, sheet-molded compounds are treated with wet finishes, which reverts back to the initial problem that gave rise to powder coating back in the ‘70s. Though some plastic surfaces can withstand the curing heat needed for powder coating, it’s still not a viable option for every plastic surface used in automotive production. The various compositions of a plastic surface make it more difficult for powder to adhere as well.
New developments in ultraviolet curing methods for powder coating plastic are addressing this challenge, however, so it won’t be long before the benefits of powder coating reach each and every aspect of new vehicles.
Industrial Powder Coating at AR Powder Coating
With the virtually limitless applications in the automotive industry and the continuously evolving methods, there’s no question that powder coating is on its way to becoming a vital technology in the world of industrial coating.
At AR Powder Coating, we offer both batch and conveyor production coatings to handle any automotive powder coating projects. We also provide masking, chemical stripping, parts and assembly and fabrication services for industrial applications.
If you’re a manufacturer interested in an industrial powder coating and want to learn more about our services, contact us to speak with a representative and get started!