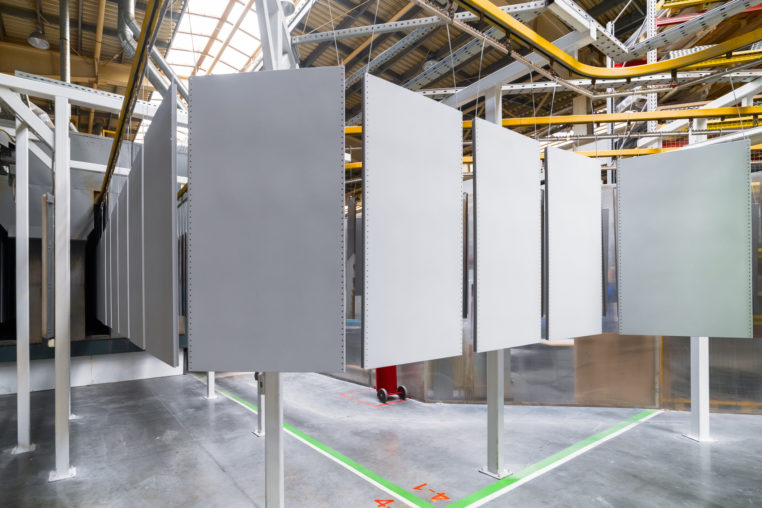
10 Ways to Fit Powder Coating into Your Supply Timeline
Powder coating is a process of applying dry powder electrostatically and curing it with heat or UV light. It has several advantages over paint, including durability, weather resistance, and customized aesthetics. Patented in 1945 for coating metal, the process has gained significant momentum with the invention of new techniques that allow powder coating to be applied to everything from appliances, to automobiles, to railings, to even plastics, composites, and carbon fiber.
Consumers increasingly prefer a powder coated finish. But as manufacturers, it might seem like an additional step to fit into your production schedule. However, powder coating can actually save you time and improve your product turnaround. Here are 10 easy ways to fit powder coating into your supply timelines.
1. Work Routinely With the Same Powder Coating Service
If you try to powder coat on a sporadic schedule with various providers, it will be difficult to quote expected delivery dates or track product inventory. Instead, partner with a comprehensive company like AR Powder Coating who can handle mass industrial coatings with an automated conveyor, as well as individual products with a batch system. Create a schedule with consistent production so you have reliable turnaround times. Use the same provider for all of your products to optimize efficiency and eliminate logistical problems.
2. Stock Pre-Coated Inventory
With an adept powder coating team, you can stock popular powder coated items to swiftly meet demand. Our team has quick production times and can also fill orders quickly when demand outmatches your current supply. Since powder coating is resistant to rust, corrosion, fading, and scratches, you can safely stock products as long as needed without a decline in their appearance.
3. Make Powder Coating a Secondary Service
In addition to stocking powder coated products, offer powder coating as an optional secondary service to meet expectations. Some customers want to customize their finish and are happy to wait a bit longer to receive their products. With the variety of powder coated colors, textures, and enhancements available, you can stock items that are more likely to be purchased in standards like black powder coating, and offer distinctive colors as secondary services.
4. Choose a Company That Pre-Cleans for You
An important step in powder coating is the pre-treatment and surface preparation. To save time, choose a company that completes this step for you. AR Powder Coating uses a superior process that includes a DI rinse, degreaser, iron phosphate, and a sealer to ensure that the product has been properly prepared going into a powder coating or media blasting process. This time-saver eliminates the cleaning step for your facility and guarantees a perfect finish.
5. Partner With a Team That Assembles As Well
Powder coating often requires the disassembly or reassembly of materials. Some companies only powder coat, which means manufacturers have to take the materials apart themselves and put them back together. But AR Powder Coating is a division of AR Iron LLC, a full-service fabrication and restoration company, so we’re experts at not only assembling, but also refinishing your products. You’ll save time by choosing a one-stop-shop like AR Powder Coating.
6. Eliminate Paint Drying Times
Paint can take hours, or even days to fully dry. There’s significant time wasted between each coat of paint. But powder coating often dries within 30 minutes, and rarely requires additional coats. Rather than adding to your production timeline, powder coating actually saves time compared to painting. Once a powder coated product has been heated, it’s ready to be packed and shipped immediately, no lengthy curing time like paint. It also requires less protective measures in the shipping process.
7. Minimize Touch-Up Time
Liquid paint can pool, bubble, drip, sag, and spill. It can be a real mess. With most paint jobs, there’s additional time spent sanding and repairing pain mistakes and touching up uneven coverage. With powder coating, it’s one and done. There’s no time wasted on touch-ups or re-sanding. You get a consistent finish with the first coat. By adding powder coating to products, you expedite delivery to your customers.
8. Reduce Time Spent on Compliance
Liquid paint is more hazardous than powder coating jobs. Since liquid paint often contains harmful solvents or volatile organic compounds (VOCs), it requires preventative safety measures for breathing and adequate breaks built in for painters. It also involves additional compliance measures to meet the standards of the EPA. With powder coating, there are little to no VOCs, and it’s considered far more environmentally friendly. In fact, certain product specifications actually require powder coating. Save time by using these safer products.
9. Minimize Waste Removal
Waste removal is a costly and time-consuming process with liquid paint. Since it requires specific disposal and storage, and can’t be reused, it wastes production time. Powder coating can be easily disposed of. And it’s also reusable, because the powder can be reclaimed and reheated, so there’s often no waste to remove at all. Since the powder coating process allows overspray material to be collected and recycled, it not only saves, time, but it also increases the coating material utilization rate, which lowers the cost of materials over time.
10. Reduce Return Processing Times
The time you invest in powder coating is returned to you ten-fold in return processing time. Powder coating is resistant to rust, corrosion, scratches, UV damage, fading, peeling, and bubbling. So, the amount of returns you have to process is vastly diminished. Save time and costs by eliminating restocking, reshipping, and replacement product manufacturing when you sell powder coated products.
AR Powder Coating is committed to efficient service and superior customer care. Producing top-quality products within your supply timeline is our first priority. Other companies take 10 days to complete a job, but our turnaround time is half as long, with completion in just 5-7 days. Our streamlined system saves you time upfront, as well as in the distribution to your customers. If you’re wondering if you can fit powder coating into your production schedule, contact us for a free consultation. You’ll be surprised to see how powder coating not only fits into your timeline, it actually saves you time.